In today's competitive business world, it's not just about delivering products and services. Companies are increasingly focusing on optimizing their processes, avoiding inefficiencies, and taking quality to the next level. This is where Six Sigma plays a crucial role. đź’ˇ
This data-driven methodology has proven to be highly effective in identifying and fixing errors, as well as improving the overall performance of business processes. It also promotes a culture of data-driven decision-making.
Â
What is Six Sigma?
Six Sigma is a methodology for improving quality and processes within organizations. It helps reduce errors and defects to an extremely low level. The term "Six Sigma" refers to a statistical value that indicates this very low defect rate.
The methodology consists of several phases, also known as the DMAIC or DMADV process (Define, Measure, Analyze, Improve, Control or Define, Measure, Analyze, Design, Verify). Here's an overview:
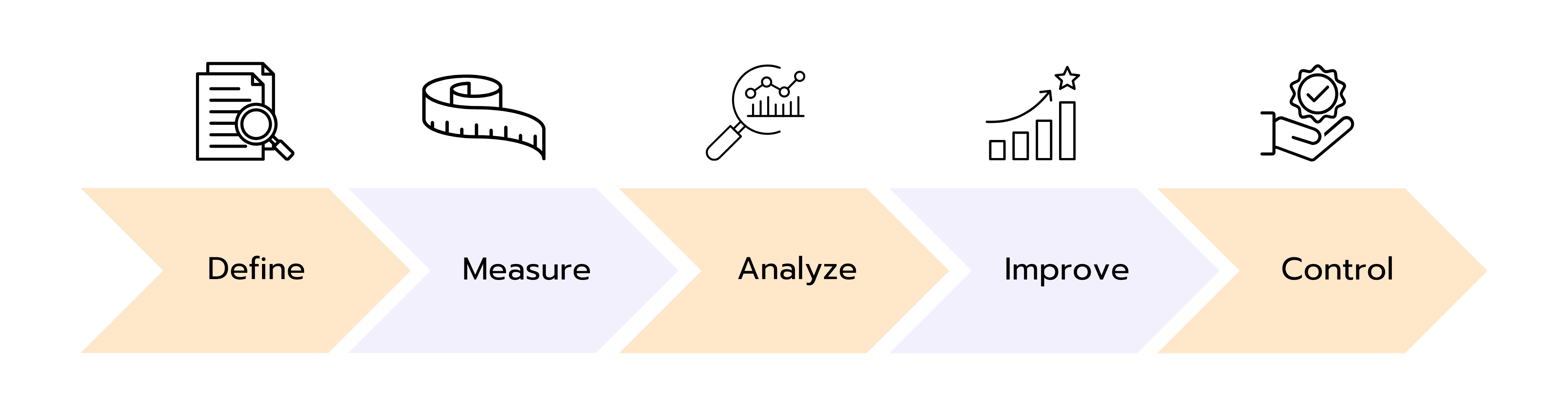
- Define: In this phase, project goals are set, relevant processes are identified, and the problem is clearly defined.
- Measure: Data is collected to understand and measure the current state of the process. Statistical analysis helps identify the causes of errors or quality issues.
- Analyze: The collected data is analyzed to find the root causes of the problems. Tools like cause-and-effect diagrams and statistical analyses are used here.
- Improve: Based on the analysis results, improvement measures are developed and implemented to optimize the process and increase quality.
- Control: After improvements are implemented, control measures are introduced to ensure the process remains stable and the quality goals continue to be met.
Six Sigma is not just a methodology but also a mindset. It’s about continuously driving improvements and eliminating errors and variations that can affect performance. The term “Six Sigma” is a metric that indicates how close a process is to perfection. This number helps companies measure and improve their performance.
Â
Who benefits from Six Sigma?
Six Sigma is applicable across industries and offers advantages in many areas. Whether in manufacturing, healthcare, finance, or software development, the methodology has shown to be effective in various sectors. Whether you're working in a startup or a large international company, Six Sigma principles can help improve operations. Employees and leaders at all levels benefit from its application, as it enables them to actively participate in improvement processes and experience the benefits of higher efficiency.
Â